Introduction and application prospects of hollow drill
Hollow drill bits (multi-edge steel plate drills, also known as core drills) are efficient drill bits for multi-edge circular cutting. The drilling diameter ranges from 12mm to 150mm. They are mainly used for drilling steel components, such as steel structure engineering and rail transit. , bridges, ships, machinery manufacturing, aerospace and other hole processing fields, its drilling performance is significantly better than the traditional two-edged twist drill, with the characteristics of high drilling efficiency, light and labor-saving drilling, multi-edged steel plate drill and magnetic seat drill The matching tool can carry out multi-directional drilling of large workpieces. The operation is convenient and flexible, effectively shortening the construction time, and has become the first choice tool for drilling and annular groove processing of modern steel components
1.Influence on cuttingEdit Broadcast?
The hollow drill bit is a hole processing tool that is more suitable for portable tools. However, since the manufacturing process of hollow drills is relatively complex and they cannot process blind holes, they are not commonly used in metal cutting. They are usually only used when processing through holes of large diameter or precious metal workpieces or when the power of drilling equipment is limited. . Since there are no standard products for hollow drill bits, most hollow drill bits used for processing special materials need to be developed by ourselves.
Back angle effect
2.Effect of rakeangle on cutting force?
Changes in rake angle will affect the degree of deformation of the chip material, thereby causing changes in cutting force. The greater the chip deformation, the greater the cutting force; the smaller the chip deformation, the smaller the cutting force. When the rake angle changes in the range of 0° to 15°, the cutting force correction coefficient changes in the range of 1.18 to 1.
3.The influence of the rake angleon the durability of the drill bit?
When increasing the rake angle of the drill bit, the strength and heat dissipation volume of the tool tip will be reduced, and it will also affect the stress on the tool tip. When the rake angle is a positive value, the tool tip is subject to tensile stress; when the rake angle is a negative value, the tool tip is subject to compressive stress. If the rake angle selected is too large, although the sharpness of the drill bit can be increased and the cutting force can be reduced, the tensile stress on the tool tip will be greater, the strength of the tool tip will be reduced, and it will easily break. In cutting tests, many drill bits were damaged due to excessive rake angle. However, due to the high hardness and strength of the material to be processed, and the low rigidity of the main shaft and the entire machine of the portable drilling rig, if the rake angle selected is too small, the increase in cutting force during drilling will cause the main shaft to vibrate, and obvious vibrations will appear on the machined surface. lines, the durability of the drill bit will also be reduced.
5.Effect on cutting perormance
Increasing the clearance angle can reduce the friction between the flank surface and the cutting material and reduce the extrusion deformation of the machined surface. However, if the clearance angle is too large, the blade strength and heat dissipation capacity will be reduced.
The size of the relief angle directly affects the durability of the drill bit. During the drilling process, the main wear forms of drill bits are mechanical scratches and phase change wear. Considering mechanical abrasion and wear, when the cutting life is constant, the larger the clearance angle, the longer the available cutting time; considering phase change wear, an increase in clearance angle will reduce the heat dissipation ability of the drill bit. After the drill bit is worn, as the wear zone on the flank gradually widens and the cutting power gradually increases, the heat generated by friction will gradually increase, causing the drill bit temperature to rise. When the temperature rises to the drill bit phase transition temperature, the drill bit will appear Wear quickly.
6.Effect of sharpeningprocess
The hollow drill bit uses less quantity and the processing batch is small. Therefore, the processing technology issues should be considered when designing the drill bit, and the processing and sharpening should be achieved with common machining equipment and common tools as much as possible. Chips flow ouion performance. During the outflow process, the chips are squeezed and rubbed by the rake face, causingfurther deformation. The metal at the bottom of the chip is deformed to the greatest extent and slips along the rake face, making the bottom layer of the chip longer and forming various curled shapes. When using a hollow drill bit to drill holes, you want the chips to be cut into chips or strips to facilitate chip removal. In order to facilitate processing and sharpening, the rake face must be designed as a flat surface without a chip breaker. The rake surface does not need to be reground during use. The flank surface of a hollow drill bit is the easiest to regrind and is also the surface with the fastest wear rate. Therefore, the sharpening of the hollow drill bit is achieved by sharpening the flank surface. The secondary flank surface is divided into an internal secondary flank surface and an external secondary flank surface. From the perspective of regrinding, it is not easy to regrind the inner and outer auxiliary flank surfaces, so the auxiliary flank surfaces should be designed not to be regrinded.
7.Cutting fluid and drillbits
The main feature of the hollow drill bit is that the inner core of the hole is not cut during processing. Therefore, the cutting amount of the hollow drill bit is significantly less than that of the twist drill, and the required drilling power and heat generated during cutting are also smaller. When drilling with high-speed steel hollow drill bits, because the temperature of the processing area has a great influence on the hardness of the drill bit, coolant must be used to cool down during the drilling process (if no coolant is used, the drill bit wear will be mainly phase change wear and rapid at the beginning. wear). At first, we used external spray cooling. However, because the drill bit station is processed in the horizontal axis direction, it is difficult for the coolant to enter the cutting edge of the drill bit. The coolant consumption is large and the cooling effect is not ideal. The drill rig spindle structure has been redesigned to change the external spray cooling to internal spray cooling. The coolant is added from the core of the hollow drill bit, so that the coolant can smoothly reach the cutting part of the drill bit, thus significantly reducing the coolant consumption and improving Cooling effect.
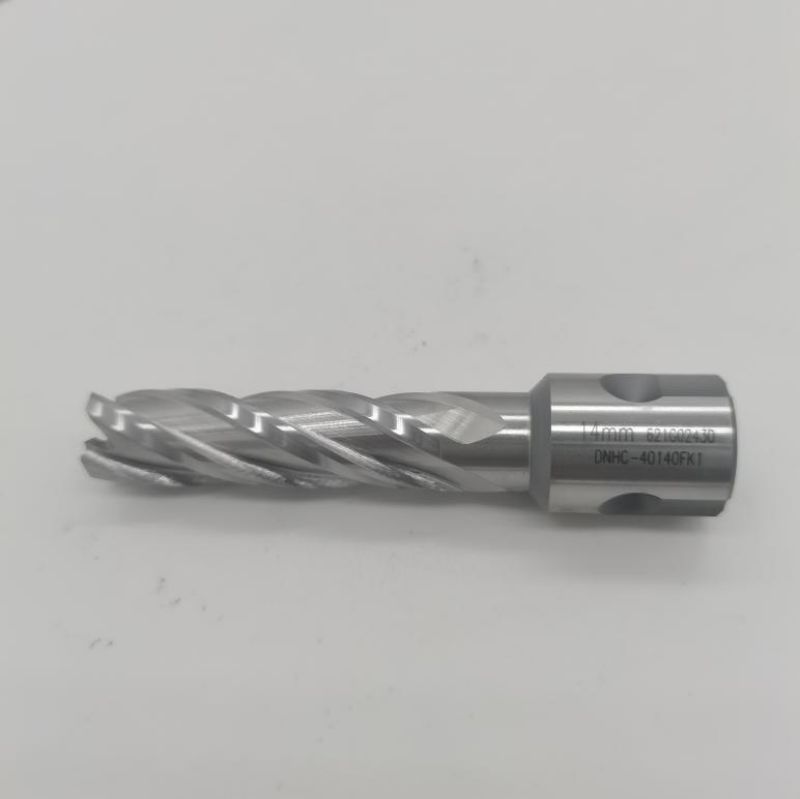
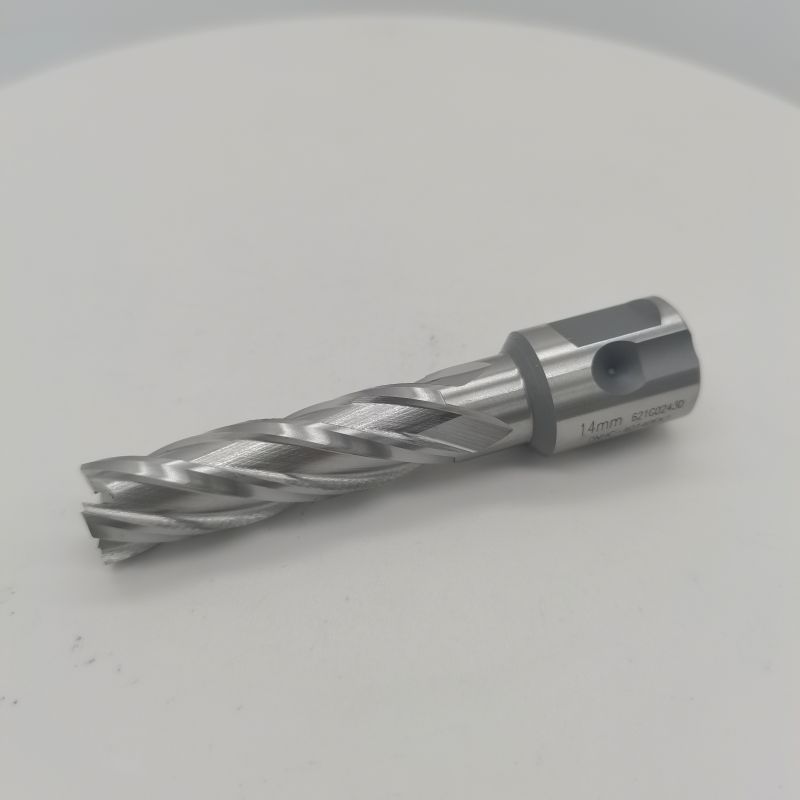
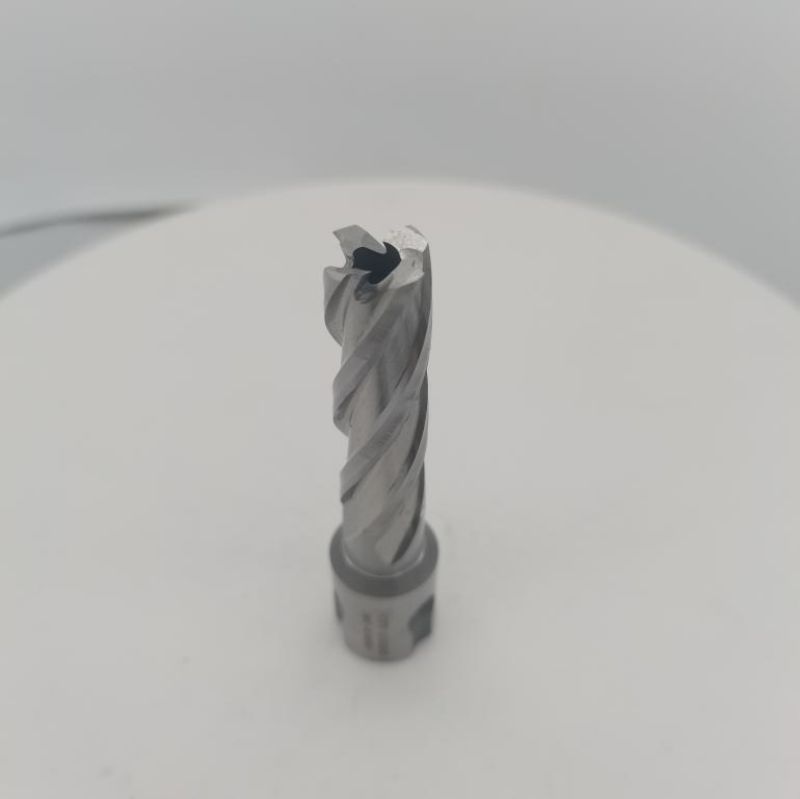